Unlocking Energy Efficiency in Manufacturing with Industrial Led Fixtures and Industry Insights
In today's fast-paced manufacturing landscape, energy efficiency has emerged as a crucial factor for competitive advantage and sustainability. According to a report by the U.S. Department of Energy, lighting accounts for approximately 15% of energy consumption in industrial settings. As industries continue to strive for operational excellence, the adoption of innovative technologies such as Industrial LED Fixtures can significantly contribute to reducing energy costs while also enhancing productivity. These advanced lighting solutions not only consume less power but also offer longer lifespans and better performance compared to traditional lighting options.
Furthermore, the Global LED Lighting market is projected to reach over $100 billion by 2024, underscoring the growing trend towards energy-efficient lighting solutions across various industries. Incorporating Industrial LED Fixtures can lead to reductions in greenhouse gas emissions and create a safer, more efficient working environment. As manufacturers seek to align with environmental regulations and meet corporate sustainability goals, leveraging the insights and advantages of Industrial LED technology will be pivotal in unlocking energy efficiency in their operations.
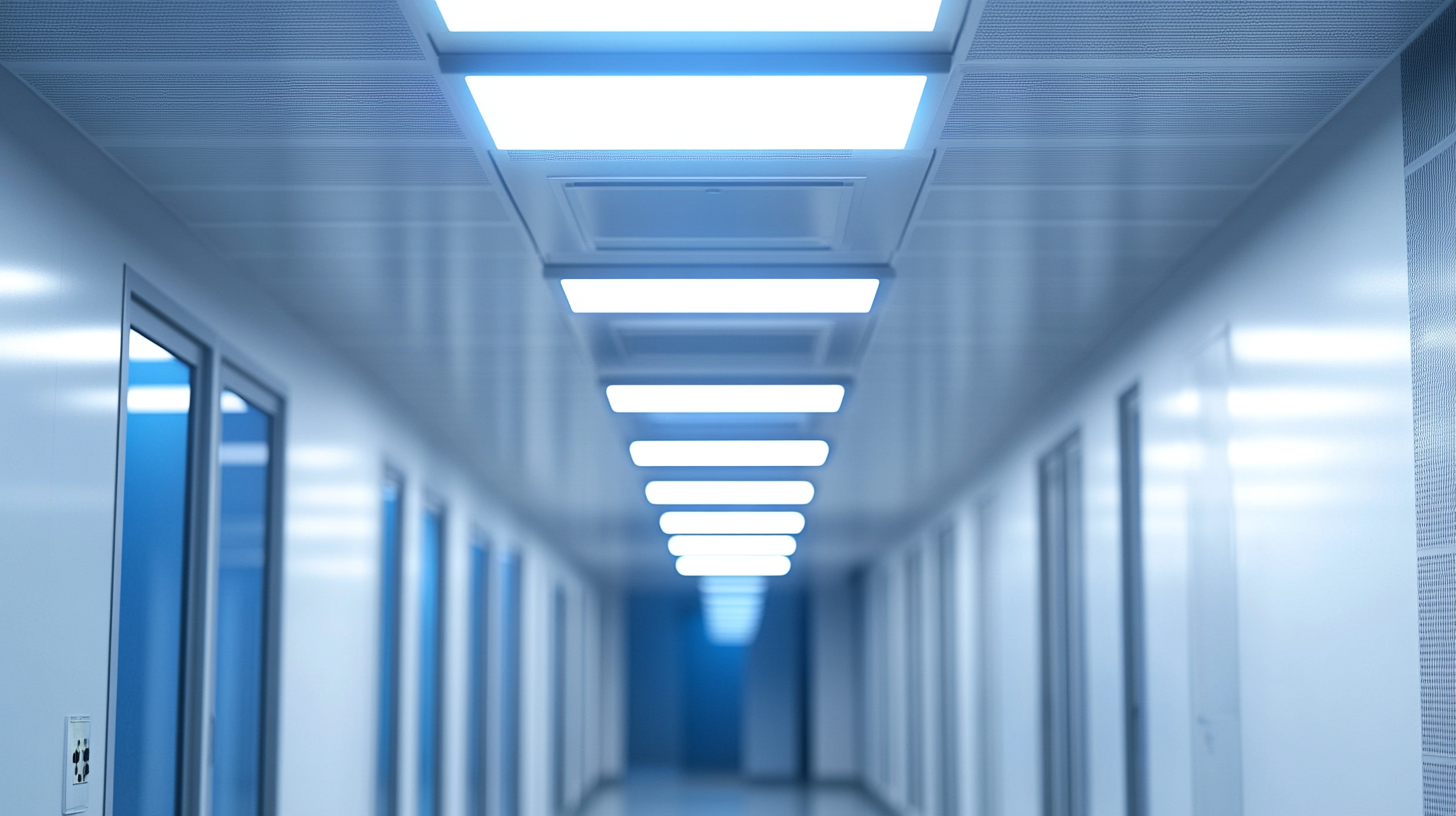
The Role of Industrial LED Fixtures in Enhancing Energy Efficiency
Industrial LED fixtures play a pivotal role in enhancing energy efficiency within the manufacturing sector. As industries strive for sustainability, the transition from traditional lighting systems to LED technology presents a significant opportunity. LED fixtures consume substantially less power while providing superior brightness and longevity compared to incandescent and fluorescent bulbs. This transformation not only leads to reduced energy consumption but also lowers maintenance costs, providing a compelling return on investment for manufacturing facilities. Additionally, integrating advanced lighting controls with LED fixtures maximizes energy efficiency. These controls—encompassing sensors, dimmers, and smart switches—allow for precise manipulation of lighting based on real-time needs. For instance, occupancy sensors can ensure that lights are only active when needed, significantly cutting down on wasted energy. The intelligent management of lighting not only contributes to cost savings but also supports the broader initiative of energy conservation, essential for sustainable industrial practices. As the global lighting market continues to grow, driven by increasing awareness of energy issues and government initiatives promoting green technologies, the importance of LED fixtures and associated controls cannot be overstated. Their adoption represents a critical step for manufacturers aiming to enhance their operational efficiency while contributing positively to environmental goals. Through the embrace of these modern lighting solutions, industries can achieve a dual benefit of improving their bottom line and reducing their carbon footprint.
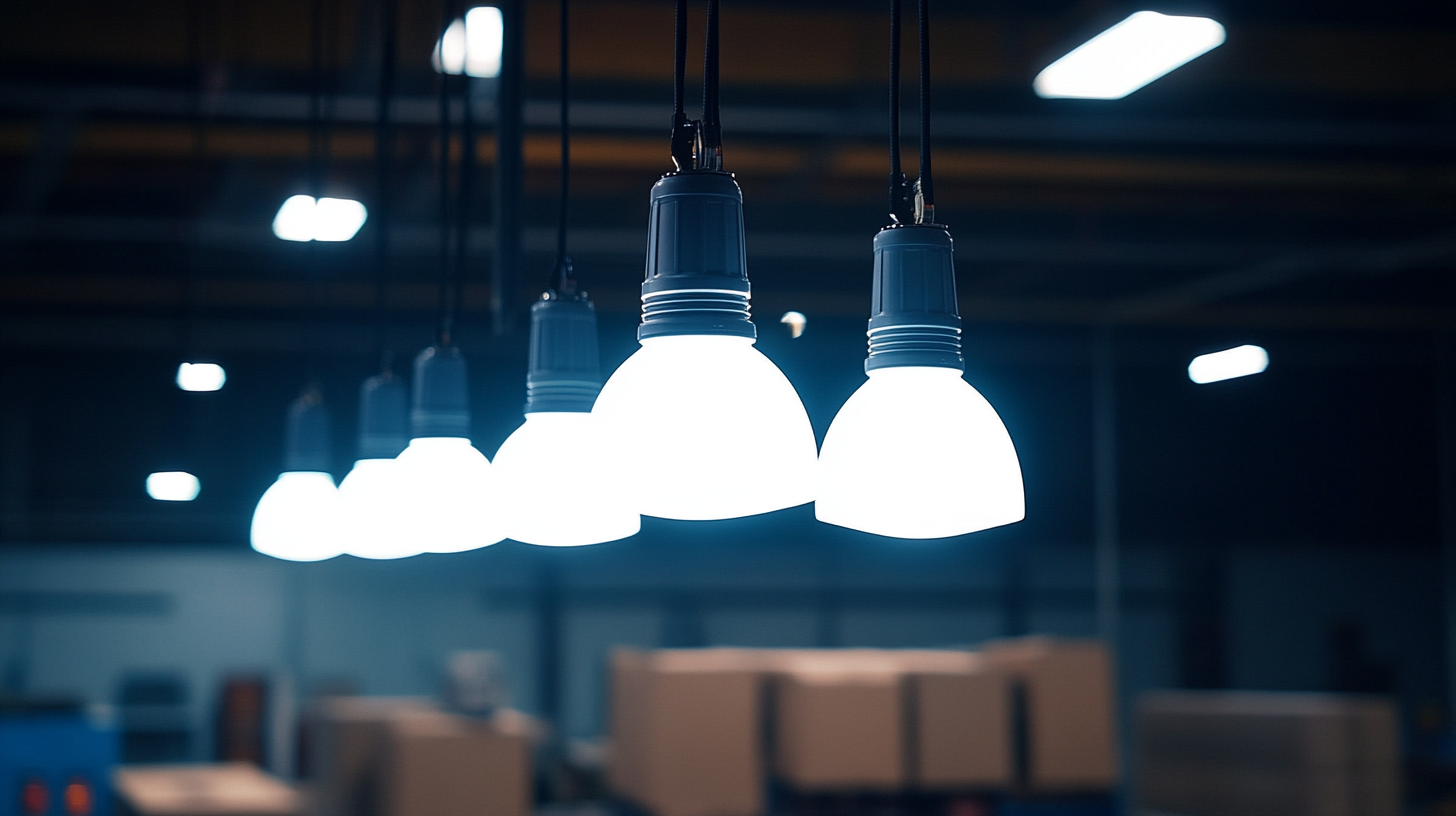
Key Benefits of Implementing LED Lighting in Manufacturing Facilities
The transition to LED lighting in manufacturing facilities offers numerous benefits that can significantly enhance energy efficiency and operational performance. One of the key advantages of implementing industrial LED fixtures is their remarkable energy savings compared to traditional lighting solutions. LEDs consume up to 75% less energy, leading to reduced utility bills. This energy reduction not only lowers costs but also aligns with sustainability goals by minimizing the carbon footprint of manufacturing operations.
Moreover, LED lighting provides superior longevity and durability, which translates to lower maintenance costs over time. Traditional bulbs often require frequent replacements, resulting in interruptions that can hinder productivity. LEDs, on the other hand, can last up to 25,000 hours or more, reducing the need for routine maintenance and allowing teams to focus on their core tasks rather than lighting upkeep. This reliability is especially crucial in demanding manufacturing environments where consistent lighting is essential for safety and efficiency.
Beyond cost savings and maintenance benefits, LED lighting enhances workplace safety and productivity. The improved color rendering and brightness of LED lights create a better-lit work environment, which can reduce accidents and errors. Workers are more alert and can perform tasks with greater precision under the bright, clear light of LEDs. As manufacturing facilities continue to prioritize efficient and safe operations, the integration of LED lighting presents a compelling opportunity to drive both energy efficiency and workplace enhancement.
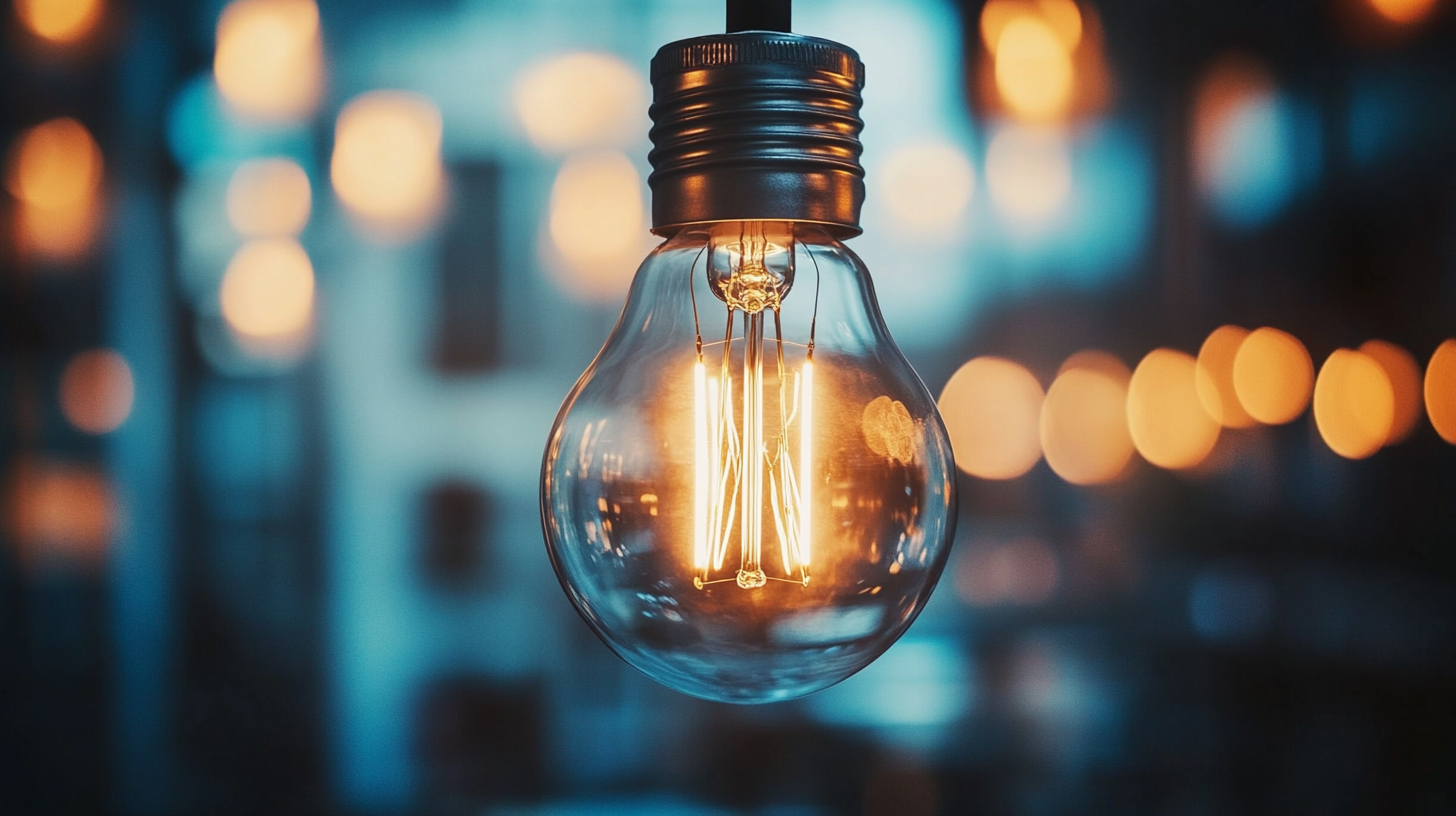
Industry Insights: Trends Shaping Energy Efficiency in Manufacturing
The landscape of the manufacturing industry is undergoing a seismic shift, driven by the need for enhanced energy efficiency. As we approach 2025, several key trends are emerging that will shape the direction of energy efficiency practices in manufacturing. Notably, data-driven strategies are paramount, with a recent report indicating that manufacturers are increasingly prioritizing investments in their digital infrastructure. This proactive approach not only fosters innovation but also helps address the ongoing skills gap prevalent in the workforce.
Additionally, spatial heterogeneity in energy utilization has become a critical focus as industrial growth accelerates, particularly in regions like China. Companies that can balance energy use with industrial agglomeration are likely to experience sustainable growth. According to industry insights, the interplay between energy efficiency and location dynamics is essential for optimizing operations and reducing carbon footprints.
The tire industry exemplifies the necessity of “green innovation” as a driving force for change. Reports indicate that businesses are no longer viewing eco-friendly practices as optional; instead, they are integrating sustainability into their core strategies to remain competitive. As companies adopt smarter manufacturing technologies, the trend of leveraging global patent strategies for innovation is becoming increasingly relevant, positioning businesses to lead in the energy efficiency arena while meeting regulatory requirements and consumer expectations.
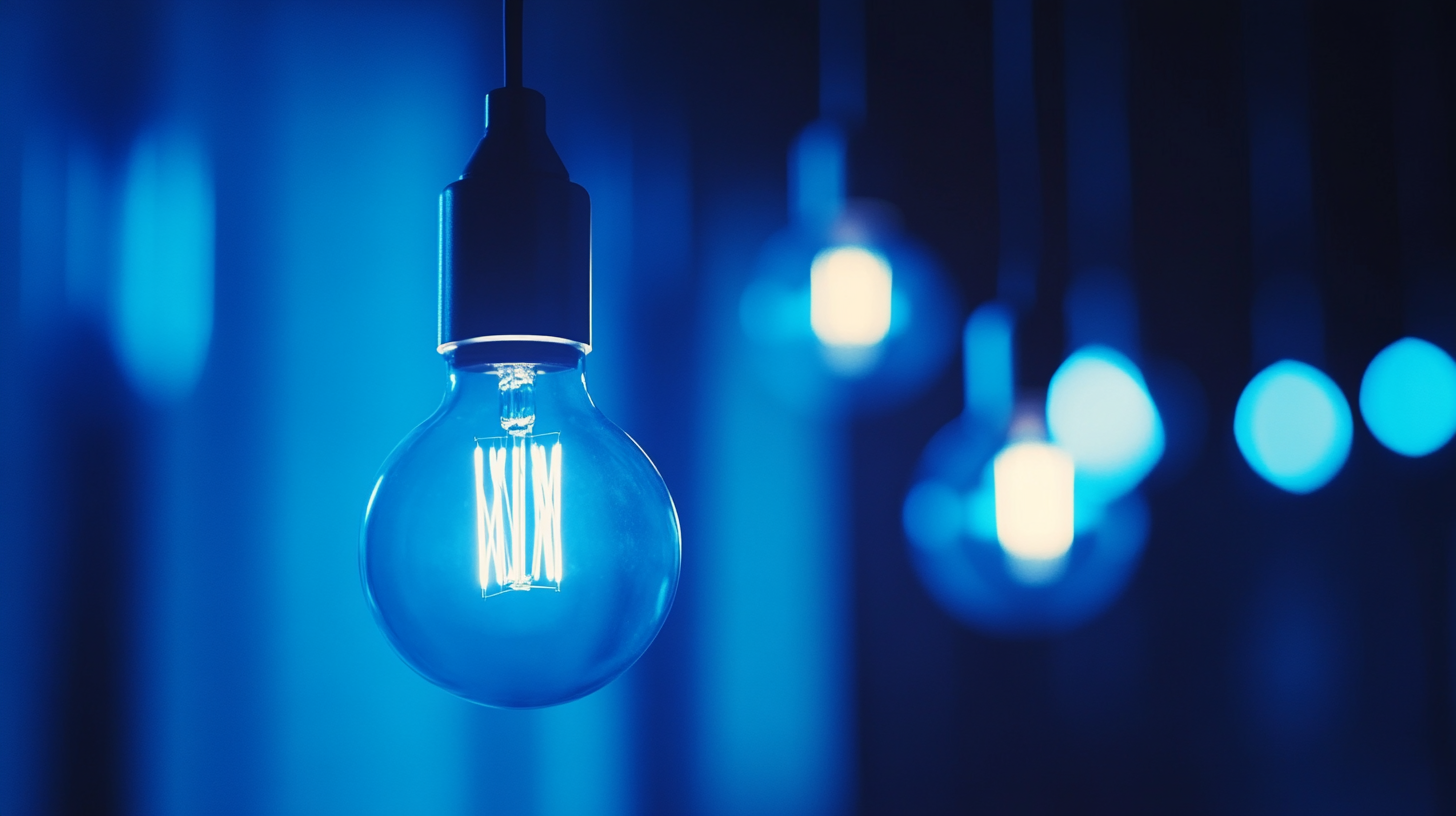
Challenges and Solutions for Transitioning to LED Lighting in Factories
Transitioning to LED lighting in manufacturing facilities has become a pressing challenge due to various operational hurdles. According to a report by the U.S. Department of Energy, industrial lighting accounts for approximately 20% of electrical consumption in manufacturing plants. This highlights the immense potential for energy efficiency improvements through the adoption of LED fixtures. However, the upfront costs of converting existing systems can deter manufacturers, with initial investments ranging from $5,000 to $100,000 depending on the scale of the operation.
Moreover, compatibility with existing infrastructure presents another significant challenge. Many factories still rely on outdated lighting technologies, which can complicate the integration of LED fixtures. A survey by the National Association of Manufacturers (NAM) found that nearly 30% of manufacturers reported issues related to retrofitting their facilities with modern lighting solutions. This emphasizes the need for tailored strategies that facilitate a smooth transition, such as phased implementation plans and comprehensive staff training programs.
To overcome these obstacles, manufacturers can leverage energy-saving programs offered by utility companies, which often provide rebates that significantly offset installation costs. Furthermore, as noted in the latest report by McKinsey & Company, organizations that incorporate smart lighting systems alongside LED technology can increase energy savings by up to 50%. Such insights underscore the importance of a strategic approach that not only considers immediate lighting needs but also evaluates long-term operational impacts and sustainability goals.
Measuring the Impact of Energy Efficiency on Operational Costs
Measuring the impact of energy efficiency on operational costs in manufacturing environments is gaining unprecedented attention, particularly as companies seek to harmonize sustainability efforts with profitability. Recent reports indicate that optimized energy use can yield substantial cost savings—manufacturers that implement energy-efficient technologies, such as industrial LED fixtures, can reduce energy consumption by as much as 75%. This shift not only leads to immediate financial benefits but also contributes to long-term operational viability by decreasing total utility costs.
In light of recent innovations, like Microsoft's new metric for assessing the environmental impact of data centers, industries are starting to recognize the broader implications of efficient energy use. According to their findings, improving energy efficiency in data centers could save the industry billions annually while reducing carbon footprints significantly. Such insights are essential as they highlight the intersection of energy efficiency with operational cost reduction, making a strong case for adopting greener technologies in all sectors.
Furthermore, systematic reporting on eco-efficiency practices, including energy and water usage, allows manufacturers to track progress and make informed decisions. Data indicates that firms that actively monitor their environmental performance see not just enhanced sustainability metrics but also improvements in profitability margins. The adoption of innovative lighting solutions, alongside comprehensive tracking systems, is proving to be a benchmark for future success in manufacturing, facilitating a path that benefits both the planet and the bottom line.